Ancoraggio Pilastri
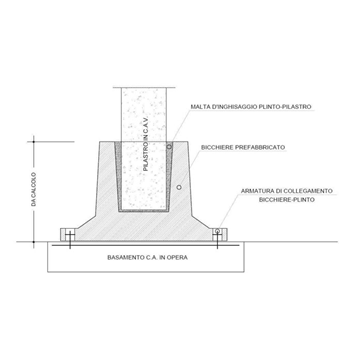

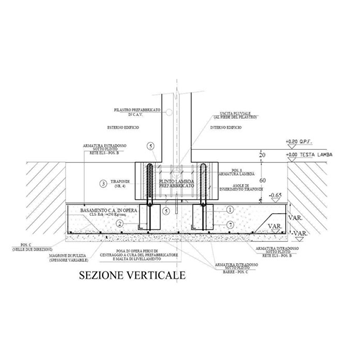
Le normative introdotte dai recenti decreti, in attuazione prevalentemente di disposizioni di armonizzazione a norme di carattere europeo, presentano delle novità sostanziali che costituiscono una vera e propria rivoluzione concettuale rispetto alle norme fino ad oggi operative.
La novità sostanziale è costituita dal passaggio da una norma essenzialmente prescrittiva ad una norma che privilegia l’aspetto prestazionale delle strutture.
La conseguenza immediata di tale approccio al problema è una spinta incentivante alla ricerca costante e metodologica di soluzioni conformi allo spirito della norma stessa ma prestazionalmente più efficaci in senso lato;
A tale scopo le presenti note hanno il compito di fornire gli strumenti necessari alla conduzione di un’efficace analisi critica circa gli attuali sistemi di ancoraggio tra strutture di elevazione e opere fondazionali; tali strumenti dovranno in definitiva permettere la scelta della soluzione ottimale da adottarsi in relazione alle diverse condizioni al contorno (fondazioni dirette, indirette, ecc.).
Le presenti note illustrano e valutano, sotto l’aspetto tecnico-economico, lo stato dell’arte nella realizzazione del nodo di vincolo tipo incastro tra opere fondazionali e strutture in elevazione (pilastri prefabbricati).
La soluzione tradizionale e di più lunga sperimentazione per tale tipo di vincolo è quella costituita dal bicchiere realizzato in opera su dado di fondazione sia essa diretta che indiretta (su pali) entro il quale procedere all’inghisaggio del pilastro prefabbricato; tale soluzione pertanto non necessita di particolari analisi o valutazioni in considerazione della conoscenza diffusa dei suoi parametri sia tecnici che economici.- Uno degli aspetti comunque più penalizzanti di tale soluzione è la realizzazione del bicchiere che necessita di posizionamento delle armature verticali del bicchiere stesso già nella fase di getto dei basamenti (con le conseguenti indeterminazioni legate alle diverse tolleranze di lavorazione dei basamenti rispetto ai bicchieri) ed il successivo completamento delle armature, casseramento, getto e scassero.
Si procede pertanto all’analisi di sistemi alternativi a quello tradizionale suddetto che non presenta aspetti tecnico-qualitativi necessitanti di chiarimenti ed analisi che non siano già abbondantemente noti.
Limitiamo pertanto la nostra analisi comparativa ai seguenti sistemi tipologici più comunemente utilizzati:
A) Plinto prefabbricato autonomo;
B) Plinto prefabbricato collegato al piede del pilastro;
C) Bicchiere rovescio;
D) Sistemi industrializzati con tirafondi;
DESCRIZIONE DEI SISTEMI
A) BICCHIERE PREFABBRICATO
Tale sistema sostanzialmente si riduce alla prefabbricazione di un bicchiere da ancorare in cantiere alla testa di basamento parallelepipedo dotato di opportuni ancoraggi (di solito armature complementari di continuità strutturale) gettato in opera e costituente l’elemento strutturale di trasmissione delle sollecitazioni al terreno (fondazioni dirette) o all’ulteriore fondazione profonda (fondazioni indirette).- Tale sistema costituisce un ulteriore passo in avanti verso la totale prefabbricazione strutturale; In pratica, sotto l’aspetto prettamente statico-funzionale, la soluzione è tecnicamente analoga al bicchiere realizzato in opera col vantaggio che le operazioni di cantiere si esauriscono nella realizzazione del basamento e nel successivo getto di inghisaggio apportando una notrevole riduzione dei tempi lavorazione in cantiere .
Uno svantaggio di tale sistema è costituito dall’eccessivo ingombro in altezza, maggiore di qualunque degli altri sistemi oggetto della presente analisi;
infatti al valore dell’inghisaggio teorico (affondamento pilastro) si deve sommare lo spessore della solatta inferiore del bicchiere prefabbricato – vedasi scheda funzionale allegata.
B) PLINTO PREFABBRICATO "LAMBDA"
Tale sistema, brevettato come plinto “LAMBDA”, costituisce in realtà una trasposizione in chiave di calcestruzzo armato, del nodo tradizionale al piede delle strutture metalliche (piastra al piede con tirafondi);
l sistema funzionalmente illustrato negli allegati grafici – prevede la realizzazione di una “piastra” in c.a. di diverse dimensioni e spessore costante non inferiore a 60 cm., gettata in stabilimento di prefabbricazione all’estremità inferiore del pilastro e dotata di aree (asolature) predisposte per l’inserimento di armature di
collegamento (tirafondi) ad un basamento debolmente armato (armature in quantità di circa 30 kg/mc. di calcestruzzo) da realizzarsi in opera con funzioni esclusive di trasmissione del carico al terreno di fondazione (caso di fondazioni dirette) e di ancoraggio realizzato direttamente alla testa dei pali nel caso di
fondazione indiretta.
Tale sistema ha il vantaggio, rispetto alla tradizionale soluzione a bicchiere, di ridurre nettamente i tempi di lavorazione in cantiere per la realizzazione degli stessi plinti a bicchiere (la realizzazione del bicchiere in cantiere è, come detto, di certo l’operazione più costosa sotto l’aspetto della durata dei lavori e del rispetto delle tolleranze di produzione e la sua limitazione alla sola realizzazione di un basamento parallelepipedo debolmente armato comporta benefici economici notevoli).
Avvenendo il fissaggio plinto Lambda – sottofondazione attraverso l’inserimento di armature in asole del plinto prefabbricato e del basamento di sottofondazione, l’operazione in virtù della presenza delle suddette asole, amplia lo spettro delle tolleranze accettabili richiedendo quindi una minore “precisione” nella realizzazione delle opere di sottofondazione; ciò è tanto più necessario e gradito se si considerano le difficoltà operative che si incontrano usualmente in cantiere specialmente nelle fasi iniziali delle lavorazioni a causa di aree, a volte, ancora non spianate e regolarizzate e che rendono difficile il rispetto delle tolleranze di produzione richieste.
Tecnicamente il sistema offre le più ampie garanzie circa la conformità al vincolo teorico progettato (incastro al piede); anzi tale rispondenza al vincolo teorico di progetto è sicuramente più elevata in tale sistema rispetto a qualunque altro dei sistemi oggi tecnicamente più in uso e descritti in tali brevi
note.
Ciò è tanto più vero se si pone attenzione alle prescrizioni operative che che la normativa vigente per le strutture prefabbricate (CNR 10025/84 e s.m.i.) detta per il vincolo al piede dei pilastri; in essa si raccomanda la realizzazione di superfici non lisce nell’area di contatto bicchiere-plinto (area di inghisaggio) al fine di migliorare le condizioni di resitenza allo scorrimento e quindi una maggiore rispondenza alle condizioni di vincolo teorico imposto (incastro al piede).
C) BICCHIERE ROVESCIO
Tale sistema rappresenta un’interessante evoluzione del bicchiere tradizionale; in sostanza il bicchiere, anziché essere realizzato in opera, si realizza nel pilastro prefabbricato (vedasi schema allegato);
Tale sistema richiede una certa attenzione nel suo impiego soprattutto quando le dimensioni della sezione in pianta del pilastro risulti non ecccessvamente grande (diciamo, in via del tutto indicativa: che sezioni al sotto di 70x70 cm. devono attivare metodologie di controllo e di calcolo più rigorose);
ciò perchè la sezione resistente al piede, con le rispettive armature, diventa la sezione del “pilastro” fuoriuscente dal basamento di fondazione che tende sempre più ad allontanarsi dal comportamento di vincolo teorico di “incastro” per trasformarsi, mano a mano che la sezione orizzontale si riduce, a vincolo reale di “cerniera plastica”.- Risulta evidente come tale comportamento della struttura debba essere assolutamente evitato mediante un controllo rigoroso delle condizioni di lavoro del nodo.
Un parametro, tendente al miglioramento delle caratteristiche funzionali del nodo, è quello di migliorare le caratteristiche di aderenza del getto d’inghisaggio ricorrendo alla scabratura artificiale della superfcie interna del bicchiere (vedi illustrazione allegata).
Tale accorgimento va, altresì, nella direzione delle prescrizioni di cui alla citata normativa CNR per il miglioramento delle caratteristiche di resistenza allo scorrimento ed in generale al miglioramento della collaborazione strutturale tra diversi elementi (pilastro-plinto).
Il sistema prevede il posizionamento in opera, in fase di realizzazione della fondazione, delle armature di attesa fuoriuscenti dallo stesso basamento; in relazione alle esigenze strutturali di limitare al massimo lo spazio tra armature di attesa e bicchiere nel pilastro, le tolleranze di produzione (leggasi: tolleranze nel posizionamento in opera delle armature di attesa) sono estremamente limitate; ciò comporta una maggiore attenzione nella fasi di spicccato e posizionamento delle armature; ovvero nelle condizioni operative di cantiere più difficili ove il rispetto di tolleranze di produzione molto strette è di più difficoltosa attuazione.
Un buon pregio del sistema è la sua capacità di limitare al minimo gli ingombri delle opere fondazionali (nella sostanza lo spessore totale del pacchetto di fondazione diminuisce dell’altezza del bicchiere rispetto al sistema tradizionale e dello spessore della “piastra” prefabbricata nel caso del sistema lambda).
D) SISTEMA INDUSTRIALIZZATO CON TIRAFONDI
Le industrie che operano nel campo della fornitura di inserteria per la prefabbricazione di manufatti in calcestruzzo hanno immesso sul mercato, ormai da qualche anno, sistemi industrializzati di collegamento di pilastri prefabbricati; tali sistemi, all’estremità inferiore del pilastro, sono un’estensione tecnologica dei sistemi di inghisaggio tradizionali di strutture metalliche mediante piastra la piede e tirafondi fuoriuscenti dalle strutture in c.a. di fondazione;
Il sistema prevede il posizionamento in opera dei tirafondi (HAB nel sistema Halfen) fissati su dima metallica; i corrispondenti inserti, dotati di asola al piede (HCC nel sistema Halfen), sono inseriti al piede del pilastro in stabilimento di prefabbricazione nella fase di produzione del pilastro stesso (vedasi schema funzionale allegato).
Il sistema presenta i vantaggi del precedente sistema a bicchiere rovescio in relazione alla limitazione dello spessore del pacchetto di fondazione e gli stessi inconvenienti legati alla necessaria richiesta precisione nel
posizionamento dei tirafondi (leggasi: tolleranze di produzione).
La realizzazione a perfetta regola d’arte del sistema ed il suo corretto dimensionamento garantiscono la congruenza del vincolo reale con quello teorico di incastro al piede anche in presenza di limitati bracci delle forze interne conseguenti a sezioni orizzontali ridotte del pilastro.
Il sistema può avere qualche limitazione nell’uso soprattutto in presenza di necessità di assorbimento di notevoli valori dello sforzo di taglio; in tal caso si rende necessario ricorrere a sistemi integrativi ai quali affidare l’assorbimento delle suddette sollecitazioni taglianti (dente di taglio). Tale aspetto è significativo, ed assume carattere di preminenza, in zone ad alta sismicità.
CONCLUSIONI
Dalle brevi note suddette si evince come la scelta della tipologia di ancoraggio al piede di pilastri prefabbricati risulti condizionata da aspetti e parametri diversi ed il più delle volte anche contrastanti;
In ragione di quanto sopra si sono forniti gli strumenti necessari al fine di permettere un approccio sistematico alla scelta tecnico-economica più idonea.
Da quanto si evince la scelta finale risulta enormemente condizionata dalle condizioni al contorno del cantiere (es.: tipo di fondazione diretta o indiretta, agibilità del cantiere, tempi d’esecuzione dell’opera, ecc.); altri parametri condizionanti la scelta esulano da considerazioni puramente tecniche per inserirsi nel più ampio contesto economico dei costi di costruzione.